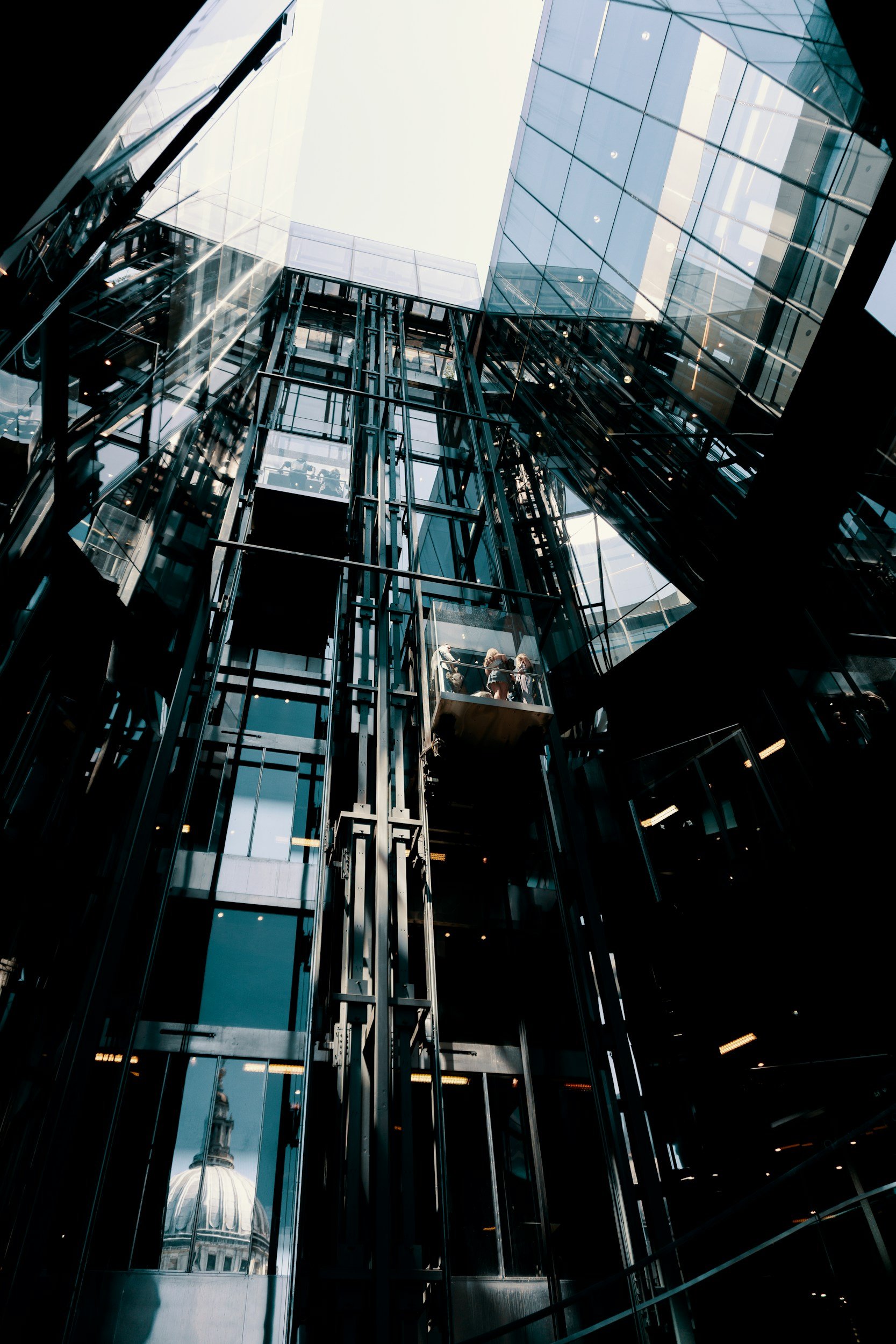
We create the world’s leading software for elevator traffic analysis
and management.
Our flagship product, Elevate, is used every day by companies in over 90 countries to simulate, record and analyse millions of passenger elevator journeys. It’s the worldwide industry standard for elevator traffic analysis software.